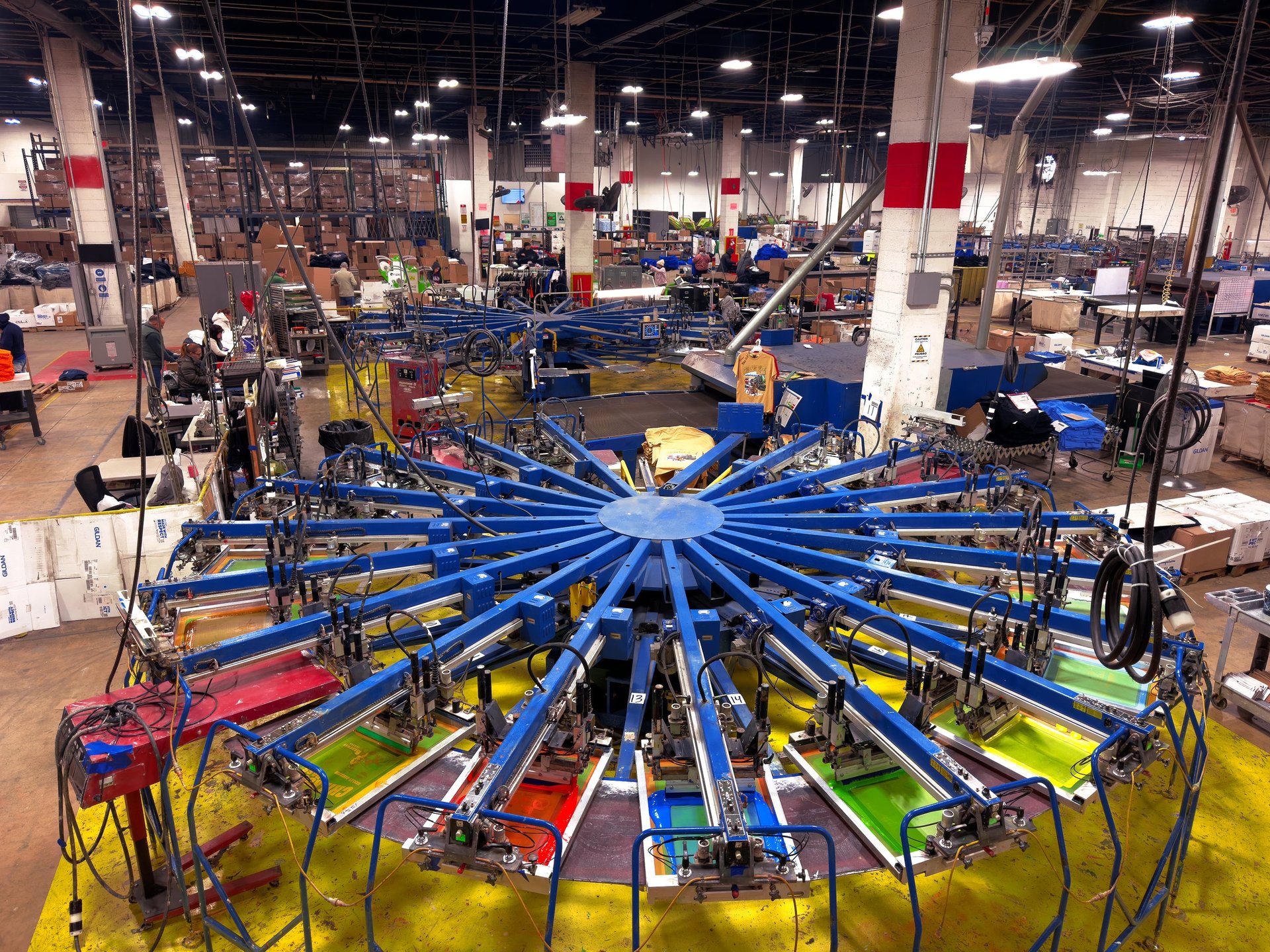
PLASTISOL TRANSFER PRINTING
Instead of traditionally screen printing directly onto apparel, screen print transfers are first printed onto a transfer paper using the same plastisol ink. The paper has a release coating that lets the plastisol ink peel off of the transfer and bond to the fabric.
Screen printing is proven technology that has been around for a very long time. The first images screen printed onto fabric took place over 1,800 years ago in China! Screen print heat transfers weren't invented until the 1960s.
Plastisol is made by combining a white powdery PVC Resin with a thick clear liquid called Plasticizer. The colors that you see come from mixing pigments into the ink. Plastisol needs to be heated to 300-330º F in order to cure (our fancy term for drying). We start every factory tour by warning not to touch plastisol because it won't dry and it won't come out of your clothes. Because plastisol does not dry or cure under room temperatures it is very shelf stable. Leftover plastisol can be stored and used for the next project. This eliminates waste.
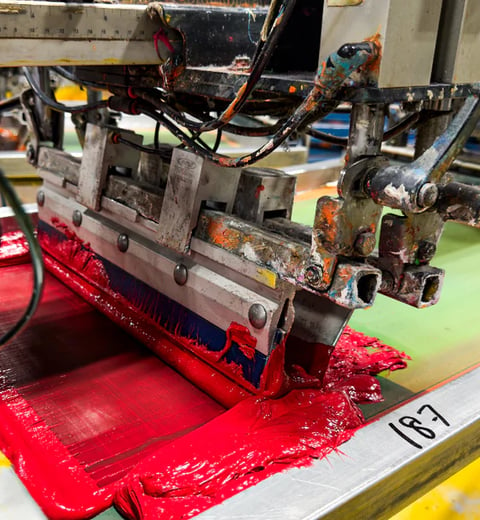
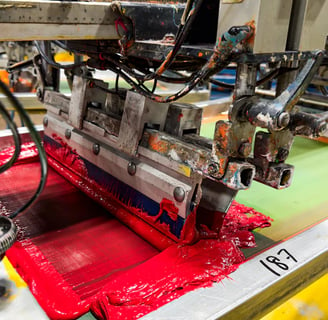
Once the adhesive has been applied to the garment, a sheet of thin foil-type is then placed over the top of the glued area and pressed using an industrial heat-press. This technique works best on standard 100% cotton products, for example, T-Shirts, sweatshirts, hoodies, polos and many more products.
It is also a great option for tote bags and similar items that are great for promotional use. Check out our diverse Promotional Merchandise offer!
Foil Printing on T-Shirt.
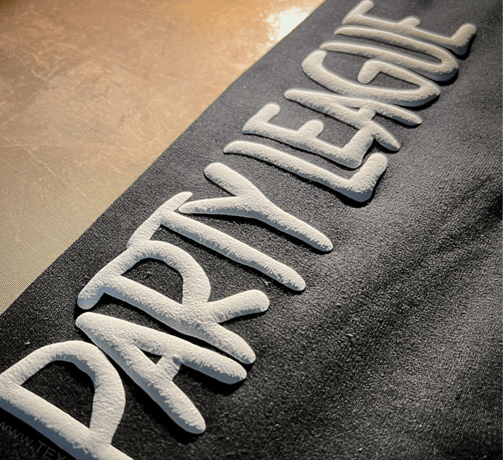
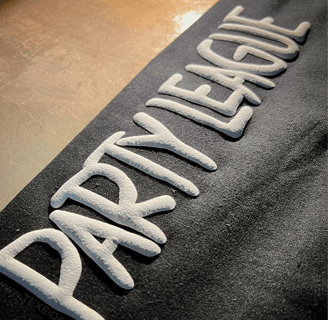
PUFF Printing on T-Shirt.
If you’ve been paying attention you’ve seen that more and more streetwear brands are bringing back the Puff prints. This type of print transfer has been modified with the addition of a heat reactive foaming agent that makes the ink expand to give you that ‘Puffy’ look.